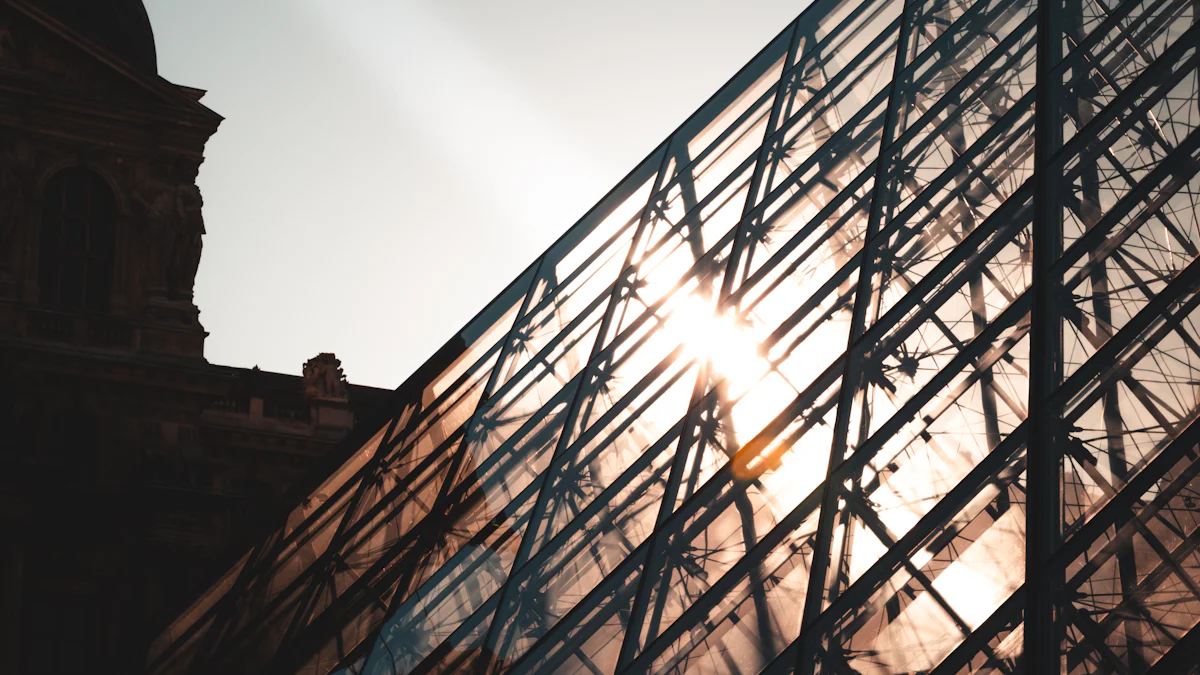
Shackles play a vital role in industrial lifting. These small yet powerful tools connect lifting equipment to loads, ensuring secure and efficient operations. You’ll find them in industries like construction, shipping, and manufacturing, where safety is non-negotiable.
Why are shackles so important? They’re designed to handle extreme forces and tough conditions. Choosing the right one matters because mismatched shackles can lead to accidents or delays. Regular inspections for wear and proper usage also keep operations running smoothly. Whether you’re lifting heavy machinery or delicate materials, the right shackle ensures safety and success.
Key Takeaways
- Bow shackles are useful and connect many slings. They work well for heavy lifting jobs.
- Dee shackles are great for straight lifting. They keep loads aligned and lower accident risks.
- Screw pin shackles are easy to use for short-term setups. They attach quickly and are simple to maintain.
- Bolt-type shackles are safer with a strong locking system. They are good for heavy-duty work.
- Chain shackles are tough and dependable. They are ideal for hard jobs and different lifting needs.
1. Bow Shackles
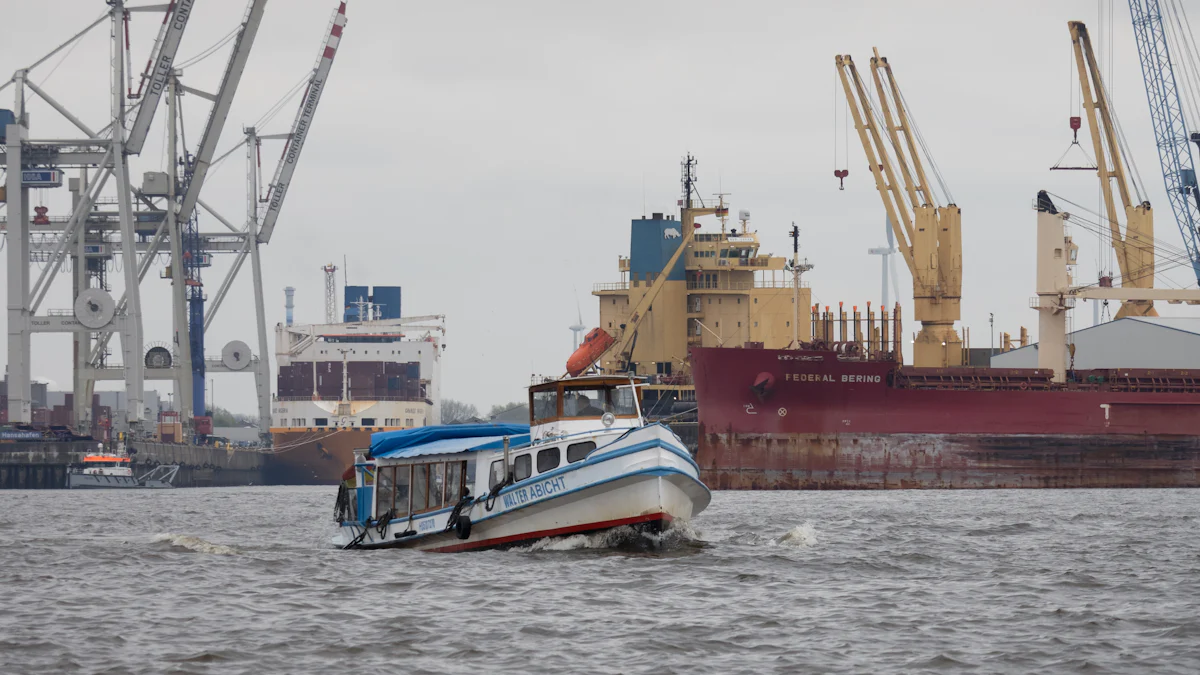
Features
Bow shackles are known for their unique design and versatility. Here’s what makes them stand out:
- A rounded, “O”-shaped bow allows for multiple sling-leg connections.
- They handle side loads effectively, making them ideal for various lifting scenarios.
- Made from high-strength materials, they resist wear and corrosion.
- Their design supports a wide range of lifting applications, from construction to offshore operations.
These features make bow shackles a reliable choice for heavy-duty tasks.
Benefits
Why should you choose a bow shackle? It’s all about safety and flexibility. The rounded bow distributes weight evenly, reducing stress on the shackle and connected equipment. This design minimizes the risk of failure during lifting. Plus, their ability to handle side loads means you can use them in complex lifting setups without worry.
Durability is another big win. Bow shackles are built to last, even in harsh environments. Whether you’re working in a factory or on an oil rig, they’ll stand up to the challenge. Their versatility also means you don’t need different shackles for every job, saving you time and money.
Applications
You’ll find bow shackles in a variety of industries, including:
- Manufacturing
- Construction
- Shipping
- Oil and Gas
- Heavy Engineering
From lifting machinery to securing loads on ships, bow shackles are everywhere. Their ability to handle multiple sling connections makes them a go-to tool for complex lifting tasks. If your work involves heavy lifting, a bow shackle is likely part of your toolkit.
2. Dee Shackles
Features
Dee shackles stand out because of their D-shaped design. This shape makes them perfect for in-line tension applications, where the load needs to stay aligned along the shackle’s axis. Unlike bow shackles, which can handle side loads, Dee shackles focus on keeping the load straight. This design prevents twisting or bending, which could compromise safety during lifting.
Another great feature is their compact and narrow body. This makes them ideal for situations where space is limited. Dee shackles are also made from durable materials, ensuring they can handle heavy loads without breaking under pressure.
Benefits
So, why should you consider using a Dee shackle? First, they’re incredibly reliable for lifting heavy loads in a straight line. Their design ensures proper load alignment, reducing the risk of accidents. You’ll also find them easier to maintain compared to other types of shackles.
Dee shackles are efficient for small to medium-weight loads, making them a versatile choice for many industries. However, their real strength lies in their ability to handle in-line tension. If you’re working on a project that requires precise load alignment, Dee shackles are your go-to option.
That said, they do have some limitations. They’re not suitable for side loading, and their narrow design means they can’t accommodate wide lifting straps. But if your job involves straight-line lifting, these shackles are hard to beat.
Applications
Dee shackles are commonly used in industries like construction, manufacturing, and shipping. You’ll often see them in action when lifting heavy machinery, securing loads, or performing rigging tasks. Their compact design makes them a favorite for jobs where space is tight.
Here’s a quick comparison to help you understand their strengths:
Shackle Type | Design | Load Capacity | Applications | Limitations |
---|---|---|---|---|
Dee Shackle | D-shaped, narrower | Suited for in-line tension | Heavy loads in a straight line | Not suitable for side loading |
Bow Shackle | Round ‘O’ shaped | Greater versatility | Various rigging applications | May not handle heavy in-line tension |
If your work involves lifting heavy loads in a straight line, Dee shackles are a reliable and efficient choice.
3. Screw Pin Shackles
Features
Screw pin shackles are a favorite for many lifting and rigging tasks because of their practical design. They feature a U-shaped body with a threaded pin that screws into place. This design makes them incredibly easy to attach and remove, saving you time during setup.
Here’s a quick breakdown of their unique features:
Feature | Description |
---|---|
Shape | U-shaped body with a threaded pin. |
Pin | Screw pin allows for quick and easy attachment and removal. |
Material | Typically made from carbon steel, stainless steel, or alloy steel. |
Applications | Ideal for temporary lifting, towing, and tie-down applications. |
Security | Regularly check and tighten the pin to prevent accidental loosening. |
These shackles are built to handle tough jobs while offering the flexibility you need for temporary setups.
Benefits
Why should you consider screw pin shackles? Their biggest advantage is convenience. You can quickly attach or detach them, making them perfect for temporary lifting or towing tasks. They’re also easy to inspect and maintain. If you notice the pin loosening, you can simply tighten it on the spot.
However, they’re not ideal for permanent installations. The pin can loosen over time, especially if it’s not checked regularly. But for short-term projects, they’re hard to beat. Here’s a quick look at their pros and cons:
Advantages | Limitations |
---|---|
Convenient for temporary lifting | Not recommended for permanent installations |
Easy to use in rigging tasks | Risk of the pin loosening over time |
Can be regularly inspected and tightened | Requires regular maintenance to ensure safety |
If you’re looking for a versatile and user-friendly shackle, screw pin shackles are a great choice.
Applications
You’ll find screw pin shackles in a variety of industries. They’re commonly used for temporary lifting, towing, and tie-down applications. Whether you’re securing a load for transport or setting up a rigging system, these shackles get the job done.
Their quick attachment and removal make them ideal for projects where time is of the essence. Just remember to check the pin regularly to ensure it stays secure. With proper use, screw pin shackles can handle a wide range of tasks with ease.
4. Bolt-Type Shackles
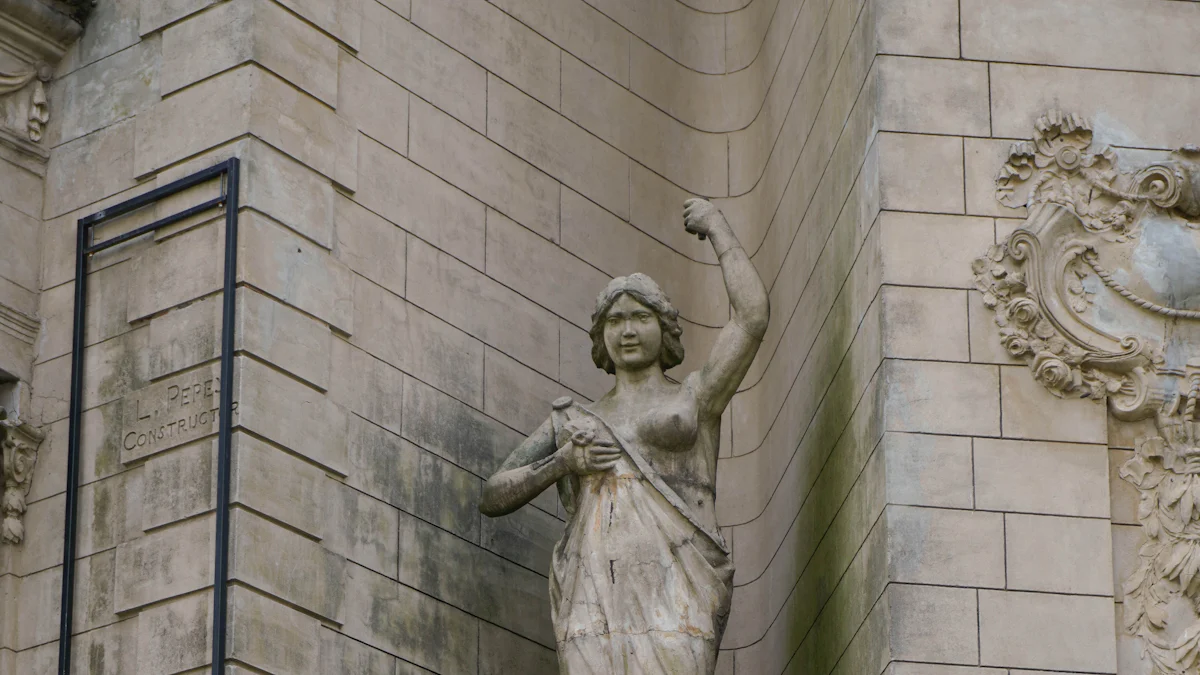
Features
Bolt-type shackles are designed with safety and reliability in mind. Their unique features make them a top choice for heavy-duty lifting tasks. Here’s what sets them apart:
- Secure Fastening Mechanism: The bolt, nut, and cotter pin combination ensures the shackle stays firmly in place, reducing the risk of accidental disconnection.
- High Strength and Durability: Made from high-strength materials like alloy steel, these shackles can handle substantial loads without compromising safety.
- Corrosion Resistance: A protective coating shields them from harsh environments, making them ideal for outdoor or marine use.
- Ease of Use: You can assemble and disassemble them without needing special tools, saving time during setup.
- Regulatory Compliance: They meet strict safety standards, including ASME B30.26 and EN 13889, ensuring reliability in critical applications.
The U-shaped body and secure pin design make bolt-type shackles a dependable choice for demanding lifting operations.
Benefits
Why should you choose bolt-type shackles? Their benefits go beyond just strength.
- Enhanced Safety: The bolt and cotter pin system provides maximum security, giving you peace of mind during lifting tasks.
- Versatility: These shackles work well across various industries, from construction to shipping.
- Longevity: Their durable materials and corrosion-resistant coating mean they’ll last longer, even in tough conditions.
- Compliance with Standards: Certifications like ASME B30.26 and EN 13889 ensure they meet industry safety requirements.
With bolt-type shackles, you get a reliable tool that prioritizes safety and efficiency.
Applications
Bolt-type shackles are a go-to option for many industries. You’ll often see them in:
- Construction: Securing heavy equipment and materials.
- Shipping: Lifting and securing cargo.
- Oil and Gas: Handling offshore containers and rigging tasks.
- Manufacturing: Supporting machinery and assembly lines.
Their ability to meet strict safety standards makes them indispensable in critical operations. For example, certifications like DNV GL and Lloyd’s Register ensure they’re suitable for maritime and industrial use.
Here’s a quick look at common safety standards associated with bolt-type shackles:
Standard/Certification | Description |
---|---|
EN 13889 | European requirements for shackle bolts |
ASME B30.26 | Rigging hardware standards by the American Society of Mechanical Engineers |
US Fed. Spec. RR-C-271, Type IVA, Class 3, Grade A | Complies with US federal specifications |
DNV GL | Certification for maritime and offshore use |
ABS | Certification for industrial standards |
Lloyd’s Register | Certification for maritime and industrial standards |
If you need a shackle that combines strength, safety, and versatility, bolt-type shackles are an excellent choice.
5. Chain Shackles
Features
Chain shackles, often referred to as D-shackles, are built for strength and reliability. Their design includes a narrow, D-shaped body that excels at handling heavy loads when the force is applied directly along their axis. This makes them a go-to choice for lifting and securing tasks in demanding environments.
What sets chain shackles apart is their construction. They’re made from materials like carbon steel, stainless steel, and alloy steel, each offering unique advantages:
- Carbon Steel: Strong and cost-effective, perfect for general use.
- Stainless Steel: Highly resistant to corrosion, ideal for marine or harsh environments.
- Alloy Steel: Extremely durable, making it suitable for heavy-duty applications.
Here’s a quick comparison of these materials:
Material | Strength | Corrosion Resistance | Best Applications |
---|---|---|---|
Carbon Steel | Strong | Moderate | General use, less demanding tasks |
Stainless Steel | Moderate | Excellent | Marine and harsh environments |
Alloy Steel | High | Moderate | Heavy-duty lifting and construction |
Galvanized Steel | Moderate | Good (zinc coating) | Economical option for lighter tasks |
This variety ensures you can choose the right shackle for your specific needs.
Benefits
Why should you consider chain shackles? Their benefits are hard to ignore:
- Exceptional Load Handling: The D-shaped design ensures maximum strength when the load is aligned with the shackle’s axis. This reduces the risk of bending or failure.
- Versatility: Chain shackles work across industries, from construction to marine operations. They’re equally effective for lifting, towing, and securing loads.
- Durability: With options like stainless steel and alloy steel, these shackles can withstand tough conditions, including exposure to saltwater or heavy wear.
- Ease of Use: Their simple design makes them easy to attach and detach, saving you time during setup.
If you’re looking for a reliable tool that combines strength and adaptability, chain shackles are an excellent choice.
Applications
You’ll find chain shackles in a wide range of industries. They’re particularly popular in:
- Manufacturing and Construction: Perfect for lifting and securing heavy machinery or materials.
- Marine Operations: Essential for securing loads on vessels, thanks to their corrosion-resistant options.
- Towing and Rigging: Ideal for connecting and securing loads in temporary setups.
Unlike other shackles, chain shackles excel at handling significant loads when the force is applied in line with their axis. This makes them indispensable for heavy lifting tasks. Whether you’re working on a construction site or securing cargo on a ship, chain shackles deliver the strength and reliability you need.
Choosing the Right Shackle
Factors to Consider
Picking the right shackle for your lifting operation can feel overwhelming, but it doesn’t have to be. You just need to focus on a few key factors:
- Weight Capacity: Always check the maximum weight the shackle can handle. This ensures it won’t fail under pressure.
- Material: Shackles come in materials like steel, stainless steel, and alloy steel. Each has unique strengths. For example, stainless steel resists corrosion, making it perfect for marine environments.
- Design and Shape: The shape matters. Bow shackles work well for multi-directional loads, while Dee shackles are better for straight-line lifting.
- Safety Standards: Look for shackles that meet industry standards like OSHA or ASME. These certifications guarantee reliability.
- Manufacturer Reputation: Stick with trusted brands. Companies with a solid track record are more likely to deliver quality products.
By keeping these factors in mind, you’ll ensure your lifting operations are both safe and efficient.
Load Requirements
Understanding load requirements is crucial. Here’s how you can determine if a shackle is up to the task:
- Safe Working Load (SWL): Most shackles have their SWL marked on them. If not, you can calculate it using the formula: D² x 8, where D is the shackle size in inches.
- Load Weight: Always ensure the load weight is less than the shackle’s Working Load Limit (WLL).
- Type of Load: Is the load static, dynamic, or subject to shock? Dynamic and shock loads require shackles with higher capacity.
- Angle of Loading: Loads applied at an angle reduce the shackle’s effective capacity. Bow shackles handle angled loads better than Dee shackles.
By matching the shackle to your load’s weight, type, and angle, you’ll avoid accidents and downtime.
Safety Standards
Safety should always come first. When choosing a shackle, make sure it meets these essential safety standards:
- Shackles must be certified for lifting and clearly marked with the WLL, manufacturer’s mark, and batch ID.
- Regular inspections are non-negotiable. Look for signs of wear, corrosion, or damage before every use.
- Always select the correct type and size of shackle for your specific load. Using the wrong one can lead to catastrophic failure.
- Environmental conditions matter. For example, stainless steel shackles perform better in corrosive environments like saltwater.
Following these guidelines ensures your lifting operations stay safe and compliant with industry regulations.
Understanding the different types of shackles can make your lifting operations safer and more efficient. Here’s why:
- You’ll select the right shackle for each task, reducing risks during lifting.
- Knowing load capacities and materials helps you optimize performance.
- Different designs suit specific applications, improving overall workflow.
Using low-quality or non-compliant shackles can lead to serious risks:
Condition | Risk |
---|---|
Heat damage | Structural integrity compromised |
Excessive corrosion | Weakening of material |
Bent or broken components | Failure during lifting operations |
Always prioritize quality and compliance to ensure safety and success.
FAQ
1. What is the difference between a bow shackle and a Dee shackle?
Bow shackles have a rounded “O” shape, making them ideal for multi-directional loads. Dee shackles, on the other hand, have a D-shaped design and work best for straight-line lifting. Choose based on your load direction and application.
2. How do I determine the right shackle size for my project?
Check the shackle’s Safe Working Load (SWL) and match it to your load’s weight. Always ensure the load weight is less than the shackle’s Working Load Limit (WLL). For angled loads, consider bow shackles for better performance.
3. Can I use screw pin shackles for permanent installations?
No, screw pin shackles are better for temporary setups. The pin can loosen over time, especially with vibrations. For permanent installations, bolt-type shackles with a nut and cotter pin offer more security.
4. Are stainless steel shackles better than carbon steel ones?
It depends on the environment. Stainless steel resists corrosion, making it perfect for marine or wet conditions. Carbon steel is strong and cost-effective but less resistant to rust. Choose based on your project’s needs.
5. How often should shackles be inspected?
Inspect shackles before every use. Look for signs of wear, corrosion, or damage. Regular inspections ensure safety and prevent accidents during lifting operations. Replace any shackle that shows visible damage or fails to meet safety standards.
🛠️ Pro Tip: Always follow the manufacturer’s guidelines for maintenance and inspection to extend the life of your shackles.